Some people say money makes the world go round. Others insist the key ingredient is love or even music. But whatever drives humanity to carry on from day to day, our dependence on fossil fuels leaves one fact for certain: The axle of our spinning globe is greased with oil.
We consume more than 102 million barrels of the stuff every day [source: IEA]. To meet our ravenous demand for fossil fuels, petroleum companies have invested billions into the development of offshore drilling operations and are constantly combing the planet for new reserves. Drill Bits For Oil Rigs
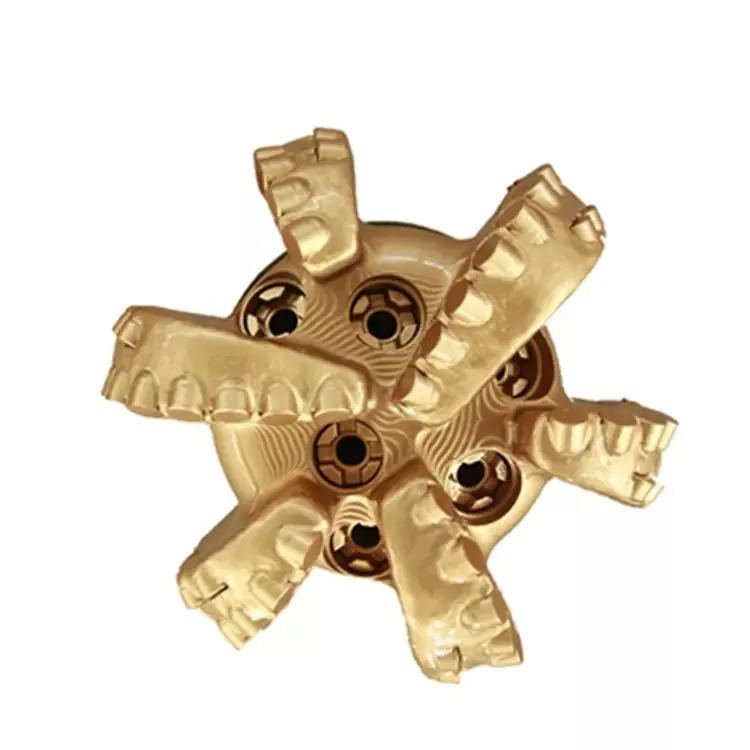
In this article, we'll examine how petroleum companies go about sniffing out this buried, black gold and the methods they use to extract it from the sea and beyond.
Since oceans cover nearly three-quarters of Earth's surface, a great deal of oil and natural gas reserves are located underwater. Reaching these undersea drilling sites poses quite a challenge. After all, drilling on land is an undertaking on its own.
How do you drill in lightless ocean depths and transport all that liquid, gas and solid petroleum back to the surface? How do you avoid polluting the ocean with oil spills? And how do you do all of this, with tons of special equipment, in the middle of rough seas?
But where there's a will, there's a way. The first offshore oil well, known as "Summerland," was drilled in 1896 off the coast of California. In the years to follow, oil prospectors pushed out into the ocean, first on piers and then on artificial islands.
In 1928, a Texan oilman unveiled the first mobile oil platform for drilling in wetlands. The structure was little more than a barge with a drilling outfit mounted on top, but it set the example for decades of advancements to come.
As time passed, petroleum companies moved even farther into the ocean. In 1947, a consortium of oil companies built the first platform that you couldn't see from land in the Gulf of Mexico. Even the North Sea, which endures nearly constant inclement weather, is currently home to many offshore drilling sites [source: The Guardian].
Today's oil rigs are truly gigantic structures. Some are basically floating cities, employing and housing hundreds of people. Other massive production facilities sit atop undersea towers that descend as far as 4,000 feet (1,219 meters) into the depths — taller than the world's most ambitious skyscrapers.
In an effort to sustain our fossil fuel dependency, humans have built some of the largest floating structures on Earth.
While fossil fuels have only become the driving force behind human civilization in the last couple of centuries, oil and natural gas have been making their way back to the Earth's surface for millions of years.
Most of the world's petroleum is trapped between 500 and 25,000 feet (152 and 7,620 meters) under dirt and rock. All of this oil began as tiny plants and animals called plankton, which died in the ancient seas between 10 and 600 million years ago. This decaying matter drifted to the bottom of the ocean and, over time, was covered with sand and mud. In this oxygen-free environment, a kind of slow-cooking process took place.
Millions of years of heat and pressure eventually transformed this organic material into vast deposits of liquid, gas and solid petroleum, all capped in traps under thick layers of rock. We call liquid petroleum oil and gaseous petroleum natural gas. Solid petroleum deposits often take the form of oil shale or tar sands.
Needless to say, these fossil fuel deposits don't just start bubbling crude every time we need to refill our gas tanks. Geologists study surface features and satellite maps, check soil and rock samples and even use a device called a gravity meter to find subtle gravitational fluctuations that might indicate a subterranean flow of oil. Not all of these options are particularly viable, however, if the terrain you're canvassing is thousands of feet below pitching ocean waves.
When searching for fossil fuels at sea, oil geologists are able to use special sniffer equipment to detect traces of natural gas in seawater. But as this method can only help find seeping deposits, oil companies largely depend on two other means of locating traps.
When close to the surface, certain rocks affect the Earth's normal magnetic field. By using sensitive magnetic survey equipment, a ship can pass over an area and map any magnetic anomalies that occur. These readings allow geologists to hunt for the telltale signs of underground traps.
Surveyors can also detect possible traps through the use of seismic surveying. This method, known as sparking, involves sending shock waves down through the water and into the ocean floor. Sound travels at different speeds through different types of rock. If the shock wave reaches a change in rock layers, it bounces back up toward hydrophones dragged behind the survey ship.
With the aid of computers, seismologists can then analyze the information to pinpoint possible traps in the Earth.
Survey ships use both compressed air guns and explosives to emit shock waves. Of these two methods, air guns are far less of a threat to sea life, but even acoustic pollution poses a threat to such seismically aware sea animals as the endangered blue whale.
What happens once survey teams detect undersea oil deposits? Well, it's time to mark down the GPS coordinates, plant a buoy and obtain a government lease to begin a little exploratory drilling and see what you've got.
Once oil companies have identified a possible undersea oil deposit, they have to obtain drilling rights. Most of the coast and ocean belong to states or nations, so companies have to lease desired areas from the respective government.
You can send shock waves down to the ocean floor all day, but ultimately you're going to have to drill a little to find out if you have a potential gusher on your hands.
To handle this job, oil companies send out a mobile drilling unit to perform exploratory drilling on a site. Some of these platforms are ship-based, but others have to be towed to the drilling site by other seagoing vessels.
An exploratory drilling rig will typically drill four temporary exploratory wells over a suspected deposit, each taking 60 to 90 days to complete. Geologists initially drill to obtain a core sample.
The principle is the same as if you stuck a hollow cylinder into a birthday cake and then removed it. You'd then be able to examine the cylinder to discover what varying layers of icing and cake existed inside the cake. Will there be ice cream? This is one method of finding out without cutting yourself a whole slice.
Of course, oil geologists aren't hoping for ice cream. They're looking for signs of petroleum, which they call a show. Once a show has occurred, drilling stops and geologists perform additional tests to make sure oil quality and quantity are sufficient to justify further action. If so, they then drill additional wells to substantiate the findings.
Once geologists have established the worth of a petroleum deposit, it's time to drill a production well and begin harvesting the riches. An average well lasts a good 10 to 20 years before it's no longer profitable, so offshore production platforms are built with a long stay in mind.
The platforms are typically fixed directly to the ocean floor using either metal and concrete foundations or tethering cables. As you might imagine, the platform has to remain as stationary as possible during all this drilling, no matter how severe the weather becomes.
One platform can boast as many as 80 wells, though not all of them go straight down. Directional drilling allows oil platforms to sink production wells into the ocean floor at an angle in order to reach deposits miles away from the drill site. If you've seen the 2007 film "There Will Be Blood," then you may know this as the "I drink your milkshake!" method. In the film, a maniacal, mustached oilman boasts that, through directional drilling, he's managed to drain all the oil beneath a nearby parcel of land.
This issue also arises in the offshore drilling industry. For instance, in California, the state can seek permission to drill new oil wells in state waters if it can prove that wells in adjacent federal waters are draining California-owned oil deposits.
Even after its wells have run dry, offshore production platforms often find renewed life as a central hub for other nearby oil platforms. The other platforms pipe petroleum over for processing and/or storage.
So you've sunk millions into erecting your oil rig. Now it's time to get busy drinking that offshore milkshake.
You've established your multimillion-dollar offshore drilling platform and, miles beneath you, there's a fortune in untapped petroleum deposits. The challenge in undersea drilling is transferring all that precious oil and gas from point A to point B without losing it and polluting the ocean.
How do you tunnel into the Earth without water flowing into the hole or all the oil surging up into the sea?
To ensure accurate drilling, engineers connect the drill site to the platform with a subsea drilling template. On a very basic level, this serves the same purpose as the templates you might have used to trace a pattern or carve a jack-o'-lantern design into a pumpkin. While the design may vary depending on the exact ocean floor conditions, the drilling template basically resembles a large metal box with holes in it to mark the site of each production well.
Since production wells often have to sink miles into the Earth's crust, the drill itself consists mostly of multiple 30-foot (9.1-meter) drill pipes screwed together, called a drill string. They're much like tent poles in this respect. A turntable on the platform rotates the drill string and, at the other end, a drill bit grinds through the Earth.
The drill bit generally consists of either a rotating bit embedded with industrial diamonds or a trio of rotating, interlocking bits with steel teeth. In the weeks or months it takes to reach the oil deposit, the bit may dull and require replacement. Between the platform and the ocean floor, all of this equipment descends through a flexible tube called a marine riser.
As the boring hole descends deeper into the ground, operators send a constant flow of drilling mud down to the drill bit, which then flows back up to the platform. This thick, viscous fluid consists of clay, water, barite and a mixture of special chemicals. The drilling mud lubricates the drill bit, seals the wall of the well and controls pressure inside the well.
Also, as the drill bit shreds rock, the resulting fragments become suspended in the mud and leave the well in the rising, return flow. On the surface, a circulation system filters the mud before sending it back down the well.
The drilling mud acts as the first line of defense against high, subterranean pressures, but there's still a high risk of a blowout of fluid from the well.
To handle these events, petroleum companies install a blowout prevention system (BOP) on the seafloor. If pressurized oil and gas gush up the well, the BOP will seal the well with hydraulic valves and rams. It will then reroute the surging well fluids into specially designed containment systems.
The drilling process itself occurs in phases. The initial surface hole, with a diameter of about 18 inches (46 centimeters) descends from several hundred to several thousand feet. At this point, engineers remove the drill string and send down hollow segments of metal pipe called casing.
Once cemented into place, this conductor pipe barrier lines the hole and prevents leaks and caving. For the next phase, a 12-inch (30-centimeter) drill bit digs the well even deeper. Then, the drill string is again removed so surface casing can be installed. Finally, an 8-inch (20-centimeter) bit bores the rest of the way to the petroleum deposit. This final stretch is called the bottom hole, and is lined with intermediate casing.
Throughout this process, a device called a packer travels down the well, expanding against the walls to ensure everything is sealed.
Once the drill hits petroleum, a final bit of casing called a production casing goes down to the bottom of the shaft. This section of casing terminates in a solid cap, closing the well off from the surrounding petroleum reservoir.
It may seem a bit odd to seal up the prize once you've finally reached it, but the goal isn't to just vent pressurized oil and gas up to the surface, but to control its flow.
Engineers send down explosives to perforate the production casing at different depths to allow petroleum into the well. This allows the oil and gas to reach the surface under less pressure, and not as a blasting geyser.
Initially, the natural pressure from the subsurface petroleum reservoir is sufficient to push fluids and gas to the surface. Eventually, however, this pressure declines, and the use of a pump or injections of gas, oil or water are required to bring the petroleum to the surface.
By adding water or gas to the reservoir, engineers are able to increase reservoir pressure, causing the petroleum to rise again. In some cases, compressed air or steam is sent down a well to heat the remaining petroleum, which also increases pressure.
If what came up from the wells was pure petroleum, it would just be a matter of barreling it up at this point. But this isn't usually the case, and it's why offshore drilling platforms often boast full production facilities as well. The liquid that rises up to the platform is a mixture of crude oil, natural gas, water and sediments. Most oil refinement takes place onshore, but oil companies sometimes use converted tanker ships to treat and store oil at sea. This process removes unwanted substances from the oil, prior to refining.
Natural gas falls into two categories: wet and dry. Wet natural gas contains various vaporized liquids, and these have to be filtered out before it can be transported elsewhere. Dry natural gas, on the other hand, is free of these pollutants. At this point, undersea pipelines and oil tankers transport the separated oil and natural gas to onshore storage and treatment plants.
Eventually, a well will either run dry, or the costs of further development will outweigh potential future profits. When this happens, petroleum companies plug and abandon the well.
At this point, operators remove platforms from their moorings — with explosives if need be — and either relocate them or drag them back to shore for scrap. Divers then cut the well casing off below the surface of the ocean floor and seal it in with concrete. In some cases, however, portions of the oil rig remain and are slowly overtaken by sea life.
Despite our culture's dependence on petroleum, not everyone's a huge fan of offshore oil drilling. Criticism ranges from dire environmental warnings to concerns over how oil rigs obstruct the view on a holiday beach trip.
The extraction of natural gas reserves via offshore drilling, particularly with the use of Mobile Offshore Drilling Units (MODUs), carries significant implications for climate and greenhouse gas emissions. Although natural gas is considered a relatively cleaner-burning fossil fuel in comparison to coal and oil, the extraction process can unintentionally release methane, an exceptionally potent greenhouse gas, into the atmosphere.
This methane leakage can manifest during various phases, including drilling, production and transportation. Because methane possesses a significantly higher heat-trapping capacity than carbon dioxide over a short time frame, even minor emissions can make substantial contributions to global warming.
Efforts to mitigate methane emissions, such as the adoption of improved drilling practices and equipment, are crucial in curtailing the climate impact of offshore natural gas extraction, particularly when utilizing MODUs.
Rigorous monitoring and effective regulation are vital to ensuring that the advantages of natural gas as a transitional energy source do not exacerbate the challenges associated with climate change.
During the exploratory drilling phase, the goals are simple: Get in, find out if there's oil and then move on to the next site. If a location proves prosperous, then the company can bring in a more permanent structure. But for the months it takes a crew to size up a location, a mobile drilling platform provides everything a team needs with minimal investment.
The cost of building jack-ups, the most common drilling rigs, can vary significantly depending on several factors, including the rig's size, specifications, features and the prevailing market conditions. As of the late aughts, they typically cost between $180 million and $190 million to build [source: Offshore Magazine].
There are five varieties of mobile drilling platforms:
Mostly used for shallow drilling in non-ocean waters, this platform is exactly what it sounds like: a floating barge with drilling equipment. Tugboats tow the platform out to the site, where anchors hold it in place. However, given that drilling barges basically just float on the surface, they're only suitable for calm waters.
This rig resembles a drilling barge, but with one exception: Once this platform reaches the drilling site, it can lower three or four massive legs into the water until they touch the bottom.
At this point, they lift the platform out of the water. This provides a much more stable environment from which to drill, as the legs stabilize the platform against winds and lift it above pitching waves. The design has its limits, however, as deeper waters require impractically large legs.
This platform combines some of the properties of drilling barges and jack-ups. Only in this case, the production facilities are elevated on stilts hundreds of feet above pontoonlike barges. After reaching the drill site, the crew floods the barges with water. The barges sink until they rest on the lake- or seafloor, while the platform remains elevated above the water on stilts.
In effect, the crew sinks the rig into order to anchor it. When the time comes for the rig to relocate, the crew pumps the water back out of the barges, causing them to float back up to the surface and push the stilted platform up into the air. Like the jack-up, this platform is limited to shallow waters.
This platform is much like a submersible rig, except it's designed to work in much deeper waters. Instead of sinking until its lower hull rests on the seafloor (which, in deeper waters, would drown everyone), it simply lets enough water in to lower it to appropriate operating heights. The weight of the lower hull simply stabilizes the drilling platform, while massive anchors hold it in place.
This is essentially an oceangoing vessel with, you guessed it, a drilling platform in the middle. The drill string extends down to the ocean floor through a moon hole. Drill ships operate in very deep water and often have to ride out rough sea conditions. They use dynamic positioning equipment to keep aligned with the drill site.
This equipment uses satellite information and sensors on the subsea drilling template to keep track of the drilling location. Using this data, electric motors on the underside of the hull constantly move the ship to keep aligned with the well. When it's time for these temporary platforms to move on, the really big rigs enter the picture.
Once the exploratory drilling phase is over and geologists have determined that a petroleum reservoir is worth the massive expense, oil companies prepare to establish an offshore production platform.
These rigs are designed to last decades, often far from land and in some of the most hostile waters on Earth. Construction crews typically build the platforms on a nearby coast and then transport them as needed to the drilling site. Production costs for these vessels typically run in the hundreds of millions of dollars.
Let's take a look at the different types of offshore platforms.
This platform design tackles the challenges of offshore drilling in the most straightforward and industrial way imaginable. Need to fix production facilities to a position above your drilling site? Why not construct a gigantic tower of concrete and steel and mount your oil rig on top?
To fully comprehend the amount of materials that go into constructing this underwater structure, consider that they operate at depths of 1,500 feet (457 meters) or less — that's just a little taller than Chicago's Willis Tower.
These platforms are extremely stable, despite the fact that the concrete base isn't even attached to the seafloor. It simply stays in place due to all the weight above it. However, at depths greater than 1,500 feet, the design begins to become more impractical due to material costs.
These rigs take the basic idea of the fixed platform and make it viable to operate in depths of 1,500 to 3,000 feet (457 to 914 meters). The design achieves this by relying on a narrower tower of steel and concrete.
But while fixed platform designs are rigid, compliant towers are designed to sway and move with the stresses of wind and sea — even hurricanes. In this respect, they're much like modern skyscrapers that are built to sway with the wind.
The Sea Star platform is basically a larger version of the semisubmersible design we talked about in the last section. The production facilities sit atop a large submersible hull on a tower.
When the lower hull fills with water, it sinks to a lower depth, providing stability while keeping the facilities high and dry. However, instead of giant anchors holding it in place, the Sea Star is connected to the ocean floor by tension legs.
These long, hollow tubes remain rigid at all times, preventing any up-and-down motion on the platform. The legs are just flexible enough to allow side-to-side motion, which helps absorb the stress of waves and wind. These platforms operate from depths of 500 to 3,500 feet (152 to 1,067 meters) and are typically used to tap smaller reservoirs in deep waters.
In the last section, we looked at some of the varieties of offshore production platforms that allow petroleum companies to reach drill sites as deep as 3,500 feet (1,067 meters).
But there's a great deal of oil under the world's oceans, and more than a few methods of reaching it. Some of these designs do away with the traditional concept of an oil platform altogether, while others elevate some of the designs from the last section to even grander proportions.
These platforms can take the form of either floating semisubmersible platforms or drill ships. The basic idea behind their design is that, once the well has been drilled, much of the production equipment can be mounted on the seafloor and the petroleum pumped to the surface facilities through flexible risers.
Meanwhile, the platform or ship stays in position with anchors or a dynamic positioning system. This approach allows oil companies to reach depths of up to 6,000 feet (1,829 meters).
This platform is essentially a king-sized version of the Sea Star platform, except the tension legs extend from the ocean floor to the platform itself. It experiences more horizontal motion and a certain degree of vertical motion, but it allows oil companies to drill at depths of up to 7,000 feet (2,134 meters), well over a mile (1.6 kilometers) beneath the waves.
This approach takes the idea of mounting the wellhead on the seafloor and applies it to even greater depths — 7,000 feet (2,134 meters) or more. Once the well has been drilled by a surface platform, the automated systems transfer the oil and natural gas to production facilities by either risers or undersea pipelines.
Finally, if you absolutely need to drill a hole at a depth of 10,000 feet (3,048 meters), then the spar platform is the oil rig for you. With this design, the drilling platform sits atop a giant, hollow cylindrical hull. The other end of the cylinder descends around 700 feet (213 meters) into the ocean's depths. While the cylinder stops far above the ocean floor, its weight stabilizes the platform.
A network of taut cables and lines trail out from the cylinder to secure it to the ocean floor in what is called a lateral catenary system. The drill string descends down through the length of the cylinder's interior and down to the ocean floor.
As technology improves and existing petroleum reserves wane, exploration will continue to dive into the subterranean depths. This combination of deeper waters and deeper oil wells will pose even greater challenges for oil companies.
Deep-sea waters reach nearly freezing temperatures, contain pressures great enough to crack iron casings and are subject to rough, deep-sea currents. Engineers have to design equipment that can stand up to the pressure, while also preventing boiling oil from hot, underground depths from cooling to a solid form and rupturing pipes when it emerges into the chilly ocean environment.
While antifreeze has played an important part in preventing this thus far, more advanced methods are under development [source: Wired].
Offshore production platforms may be marvels of modern engineering, but none of that valuable petroleum makes its way out of the wells and into refineries without a great deal of human labor. In fact, larger oil rigs often employ more than a hundred workers to keep the platform running.
As many of these rigs are located far from cities and shores, the employees (who range from engineers and geologists to divers and doctors) live for weeks at a time on these huge structures.
There are definitely pros and cons to working on an offshore platform. On the plus side, salary and benefits are usually pretty good, and employees typically enjoy long rest periods when they're not at sea. Employees will work one or two weeks on the oil rig, then spend one or two weeks at home.
The downside, however, is that when they're at sea, they work 12-hour days, seven days a week. The weeks away from home can strain workers' home lives, as they spend half the year away from their families.
To help cope with these issues, petroleum companies frequently put a great deal of effort into providing comfortable living conditions for offshore workers. In many cases, quarters are on par with those found on major cruise ships — featuring private rooms, satellite TV and even gym, sauna and recreation facilities.
The food onboard also tends to be above average — and available 24 hours a day. After all, work on an oil rig continues day and night, with employees working rotating schedules of daytime and nighttime shifts. Helicopters and ships bring in most of the necessary materials for day-to-day life on an oil rig, often through choppy weather conditions.
Oil rigs aren't all Jacuzzis and cafeterias, though.
Outside the living quarters, life on an oil rig is a constant encounter with potentially deadly conditions. The business of an oil rig boils down to drawing extremely flammable fluids out of the Earth, burning some of it off in a giant jet of flame and separating highly poisonous hydrogen sulfide gas from the extracted petroleum.
On top of this, workers have to deal with all the typical dangers associated with operating dangerous machinery and working at tall heights in windy, stormy conditions.
To cope with these dangers, petroleum companies make use of extensive training programs on how to work safely with volatile substances on the high seas. These measures not only help to safeguard the lives of their employees, but also protect their truly massive financial investment in constructing and sustaining an offshore production platform.
This article was updated in conjunction with AI technology, then fact-checked and edited by a HowStuffWorks editor.
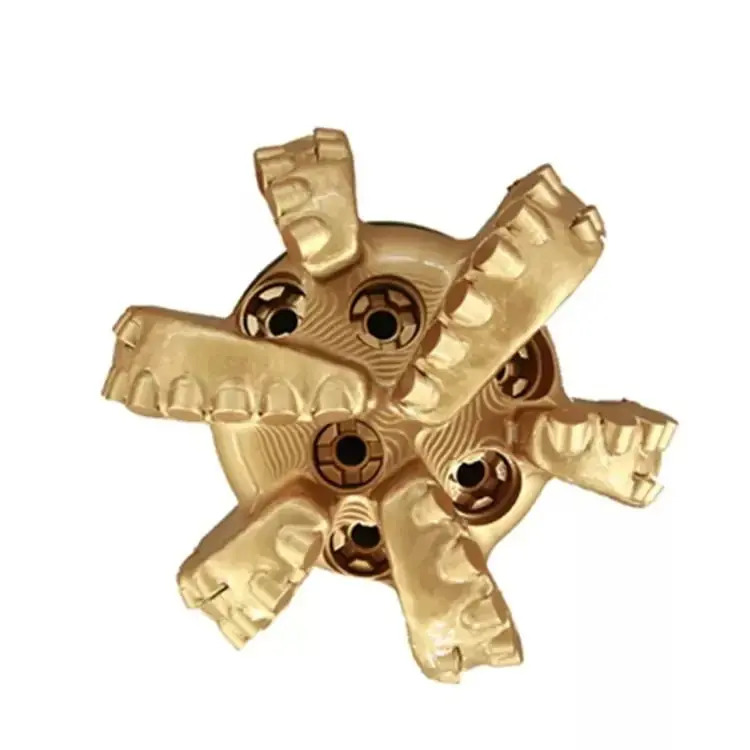
steel tooth bits iadc126 660mm Please copy/paste the following text to properly cite this HowStuffWorks.com article: