Slowing the speed of the screw will allow finer sand to be processed. Photo: EIW
Fine material washers are low-horsepower sand dewatering devices used for washing, classifying and dewatering sand in construction aggregate wet washing plants. Acrs Concrete Mesh
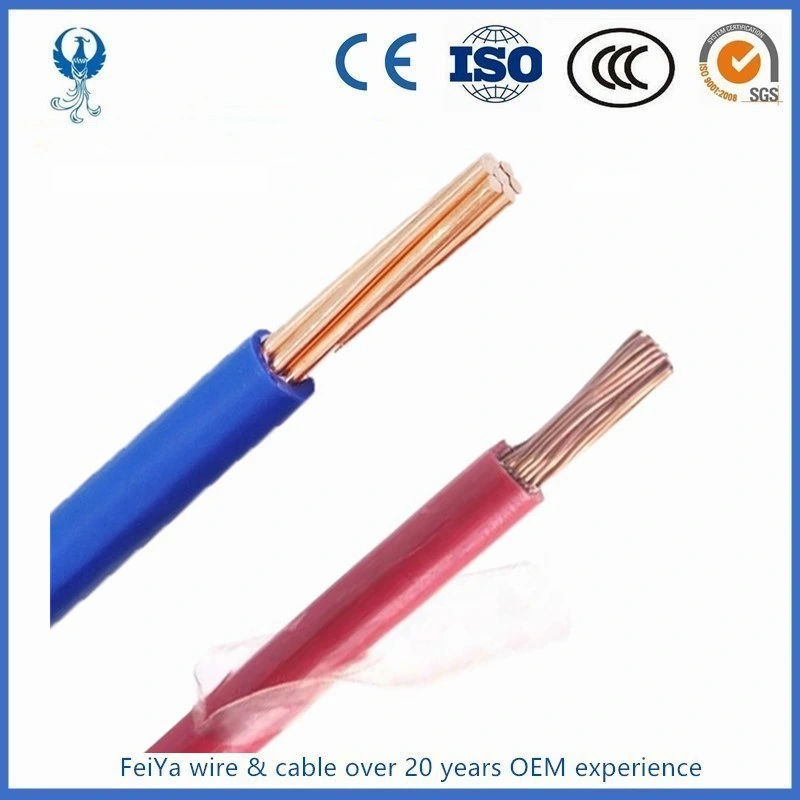
They are available in single- or double-screw configurations, with selection determined by sand solids capacity and water volume flow.
Washing is the primary function of a fine material washer. It is achieved by the continuous rotation of the conveyor shaft and the velocity of the overflowing wastewater. The rotating shaft causes feed material to roll and tumble, providing particle-on-particle attrition that allows many deleterious coatings to be removed from the sand product and discharged with the wastewater.
The second function of a fine material washer is classification. Classification is achieved by adjusting the volume of water that flows over the back and side weirs of the washer tub.
To achieve maximum material retention, the three weirs should be set level to each other to provide a low-overflow velocity. A calm pool area is key to efficient classification. This allows the product-sized solids to settle out and any fine particles to overflow with the waste.
The third function of a fine material washer is dewatering. Dewatering is accomplished by conveying the product from the washer tub up the inclined dry deck area, which allows much of the free water to drain from the material. The use of a close-clearance curved plate on one side of the dry deck area and a drainage trough on the other also aids in dewatering.
Fine material washers are a tried-and-true method for washing, classifying and dewatering sand.
While they have been used in wet processing plants for decades and many aggregate producers are familiar with how they work, here are some operational tips and best practices to help you get the most out of a fine material washer:
1. Slow the screw speed for finer sand processing. Screw speed is determined by the percent passing 50 mesh. Finer material needs more time to settle out in the washer tub, so slower screw speeds are necessary.
Screw speed can be calculated by dividing 1,500 by the percent passing 50 mesh. For example, if 15 percent of the material is passing 50 mesh, the screw should be operated at 100 percent speed for optimum operation. If the sand is slightly finer and contains 20 or 30 percent passing 50 mesh, the screw should be run slower at 75 and 50 percent speed, respectively, for optimum operation.
With excessive shaft speed, fine material can build up in the corner of the washer tub. This occurs because the screw is moving too fast for the fine sand to be conveyed toward the discharge. After a few hours of operation at excessive speeds, you will see the resulting tub corner buildup, as well as the entire pool area fill with fine sand that eventually overflows product-sized fine sand to waste.
2. Consider adding more processing steps. Additional processing steps are required when a sand feed has a high amount of minus 200 mesh or 0.075-mm material.
Generally, when you have more than 12 to 15 percent of minus 200-mesh material, you should consider a two-step process. A two-step process involves two stages of washing and can be accomplished with two screws or with a hydrocyclone feeding a screw.
3. Ensure you have enough water. Water is imperative for washing aggregate material, and you need to be sure your equipment is supplied with the appropriate amount of water for optimal operation.
As a rule of thumb, fine material washers require 50 gallons of water per minute to remove 1 ton per hour of silt.
4. Consider adding rising current. Rising current allows for fine-tuning via water injection beneath the pool areas.
The addition of clean water improves the classification process. Introducing an upward-rising current of water helps to keep the ultra fines in suspension while the product-sized particles can settle out to be conveyed out of the tub area as product.
5. Leveling the weirs. Leveling the weirs on a fine material washer optimizes performance. If you want to get rid of a small amount of excess fines, raise the side weirs and lower the back weir. This allows more velocity to overflow the back of the washer to remove excess minus 200-mesh fines.
6. Use flush water to decrease buildup. Adding water to the dry deck area of a fine material washer can result in drier sand discharging onto the conveyor and into the product pile.
How? The water flushes out any fine sand that accumulated to allow a clear channel for the water to drain from the sand as it is conveyed up the screw.
7. Ensure you have proper feed entry into a fine material washer. It’s important to have a calm pool area to ensure maximum fines retention so sand makes it to the product pile rather than overflow with the wastewater destined for the settling pond.
Too much turbulence in the feed area of the washer tub can cause the loss of excess minus 200-mesh fines and, potentially, some plus 200-mesh fines, as well. A feed chute or flume with a velocity break box allows for some turbulence, but not too much.
8. Make sure your equipment is properly lubricated. Proper lubrication of bearings is key to ensure optimal performance and unexpected downtime.
Based on a 40-hour-per-week operation, the rear outboard bearing should be lubricated every three months or after 500 operating hours. Keep in mind that overgreasing can damage the seals and plug the drainage port.
Following these eight operational tips and best practices will help your fine material washer run smoothly – with less downtime and more uptime for sand production.
Information for this article provided by EIW (Eagle Iron Works).
If you enjoyed this article, subscribe to Pit & Quarry to receive more articles just like it.
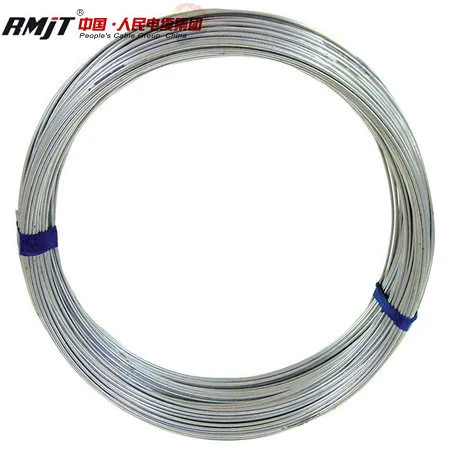
Baling Wire © 2024 North Coast Media LLC, All Rights Reserved.