We use cookies to provide you with personalized services and improve our website. More info Ok
Ortner: NKE Bearings, Austrian manufacturer located in Steyr, has established itself as a leading manufacturer of high-performance bearings, since its foundation in 1996 by a dedicated team of engineers and craftsmen. Wheel Bearing For Front Axle Transmit
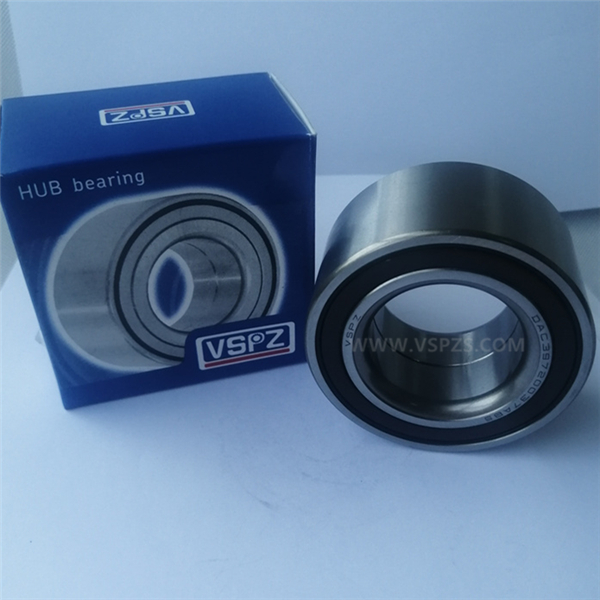
We are a leading provider of bearings for wind turbines, while also producing a comprehensive range of standard and custom bearings for all industrial applications. These bearings can be produced with short lead times and are tailored to the specific needs of each customer. Being a solution provider, a bearing is just the initial part of the value we offer to our customers, with services getting increasingly more important.
One of our key differentiators towards other manufacturers is the “best of both worlds approach” we offer. Being part of the global Fersa Group allows us to provide all the perks of a multinational company, that is vast engineering and R&D capabilities, global production sites as wells as in-depth Quality competencies. At the same time, being a family-owned business, we are fast in decision making, agile and flexible in everything we do.
Based on a deep understanding of each application, we offer customers a multitude of Engineering services – like bearing design and selection, lifetime calculations, benchmarks, FE calculations - and help them improve their process flows. Recently, we analysed the end-to-end bearing journey of a customer specialized in Wind Turbine Generator repair. Based on this exercise, together with the customer we developed customized packaging, an improved installation and handling process. On top, we trained the service personnel of the customer in their local facilities. With this, we can significantly improve the up-time of the Wind Turbine Generator creating a win-win situation for everyone.
Ortner: NKE manufactures bearings for the entire mechanical power-drivetrain of wind turbine applications, that is mainshaft bearings, gearbox bearing solutions as well as generator bearing solutions.
The bearing loads and rotating speeds vary considerably due to constantly changing winds. This means the features of wind turbine bearings is that they have to operate in a wide range of loads from light to heavy loads.
• The force that the main shaft bearing carries mainly includes the weight of the rotor and the hub, and the force of the wind acting on the main shaft through the wind rotor.
• The power of wind turbines is increasing, which means that the loads that have to be transmitted by the gearbox and its bearings are increasing too. The individual loads and requirements vary from bearing position to bearing position. i.e., planet carrier bearing’s speed is very less compared to high-speed shaft bearing speeds…
• The loads within a Wind Generator are typically not a problem.
But one of the main threats to bearings in variable-speed wind turbine generators is stray currents. If current is routed through the bearing, it can cause micro-pitting and other types of surface damage. Eventually, the bearing can fail – potentially leading to a catastrophic failure of the generator. In order to avoid this passing of the current, NKE developed the SQ77 earing portfolio, which are bearings featured with a ceramic layer on the inner or outer ring. Further we offer innovative NKE Hybrid Bearings which are featured by ceramic balls instead of common steel balls. The ceramic balls provide best insulation characteristic, but also offers a lot of other advantages, such as high-speed suitability and best dynamical behaviour due to less weight, best running noise characteristic and also and extended service lifetime under severe lubrication conditions.
Santos: As the wind turbines get bigger and bigger, it requires a completely different set of skills when it comes to production, testing, and transportation of the new products. To address this fact, we are working on different actions.
One of our approaches is developing bearings with “Power Dense” technology that can support the same load ratios as traditional bearings with a 10 to 20 percent reduction in terms of size and weight. We are also offering Sliding bearings, a technology disruption that replaces the traditional rolling bearing for a sliding surface which allows us to maintain the reliability of the application while reducing the size by 40 to 50 percent compared to a traditional bearing. In this regard, we have entered a partnership with Kugler, a Swiss producer of bimetallic components and tribological surface finishes.
Applications control and monitoring while in operations are highly demanding in both wind and rail sectors when it comes to the reliability of the application, and the customers want to maximize the operation time. To address this fact, we are working on different approaches. We have developed a condition monitoring sensor to control the performance of our bearings once they have been installed in the application from a remote location to predict potential failures. We also have launched a new product line known as Hybrid Bearing that ensures complete electrical insulation between the rotor and stator. This product line combines standard steel rings with ceramic rolling elements, ensuring electrical insulation while performing better in extreme conditions with way lower vibration and noise levels than traditional bearings.
Fast technology development that results in a short life cycle of our products is another challenge. To address this situation, we work on the flexibility of our manufacturing process together with an extremely agile engineering support. As a result, we believe we have one of the fastest time-to-market processes in the bearing industry.
Andreu: The acquisition of NKE represented a crucial and preliminary achievement in our global strategic plan. We discerned significant indicators amidst an array of complexities that required attention, including instability in the automotive market, disruptions in the supply chain caused by geopolitical issues, heightened emphasis on climate change and net-zero transition, and pronounced pricing pressures.
The inclusion of NKE within the group has resulted in a more robust local-to-local business, diversified revenue streams beyond the automotive industry, and an augmented green revenue stream, in addition to access to top talent in central Europe. As a member of the Fersa Group, NKE has benefitted from economies of scale, access to advanced technology, and capital investment to sustain exceptional growth.
Andreu: Fersa Group considers it essential to be a significant participant in the worldwide electrification of the economy. To this end, we have identified three primary areas in which we can assist in reducing carbon emissions: wind power, green transportation (including railway and electric mobility), and curbing emissions from ICE mobility.
We have already supplied bearings to the market, enabling the production of roughly 10,000 MW of wind power across Europe, Asia, and America. Furthermore, we have delivered over 30,000 bearings to renowned global brands for railway applications. Regarding these two segments, we plan to increase our manufacturing capacity by approximately 50% in 2023. Currently, we have the capability to manufacture bearings with diameters of up to 1.8M, which we intend to expand to 2.3M in the next few months.
Andreu: Currently, we are augmenting our manufacturing output and expanding the dimensions of our bearings. However, the primary challenge we face is maintaining a delicate equilibrium between increasingly stringent quality requirements and the necessity of providing a cost-competitive product.
For renewable energies to supersede conventional energy sources, their prices must decrease. This price reduction hinges on three critical factors: larger and more efficient equipment, improved performance, and reduced hardware costs.
We are truly committed to adding value to our customers while acknowledging the challenges in the industry, therefore, we are currently investing in developing advanced measurement systems and Metrology 4.0 that applies to our LSB.
At Fersa Group, we believe that the most effective means of balancing these opposing forces (i.e., enhancing performance while lowering costs) is to invest heavily in technology, both in product design and manufacturing.
Ortner: The smallest bearing in our portfolio is about 3 mm inner diameter. (623)
The largest bearing ever manufactured by NKE has about 3,3-meter outer diameter. NKE developed several special, customized bearing solutions for different industrial applications, like agriculture machinery, conveyor belts, steel mills, wind and railway drivetrains. We focus on solving customer’s problems and increase the overall reliability and efficiency of our customer’s applications.
However, one of the most outstanding special bearing solutions, developed by NKE, is the Modular Sensor System Bearing MoSS. This bearing can be retrofitted and allows monitoring of real-time operation data such as temperature and speed of the bearings to be transferred wirelessly out of the bearing to be further analysed. Companies can thus detect potential bearing problems earlier, perform predictive maintenance or optimise warranty monitoring of machines. The system is applying an energy harvesting concept and thus does not need any battery!
Graduated in political sciences and international relations in Paris, Anis joined the team in early 2019. Editor for IEN Europe and the new digital magazine AI IEN, he is a new tech enthusiast. Also passionate about sports, music, cultures and languages.
Among other advantages, NKE's black oxide finished bearings offer improved run-in and wear and enhanced adhesive wear characteristics.
Matthias Ortner is NKE’s new Deputy Managing Director in Steyr and Stefan Weidmann will manage sales.
NKE launches a development engineering department with new technological approaches
The modular bearing system for planetary gears in wind turbine gearboxes offers a standardisation of the bearings, a reduced diversity of parts and simplified logistics.
in iron or steel housings
IEN Europe spoke to Matthias Ortner, General Manager at NKE Austria and Hugo Santos, CBDO at Fersa Group.
Digital Edition Download PDF
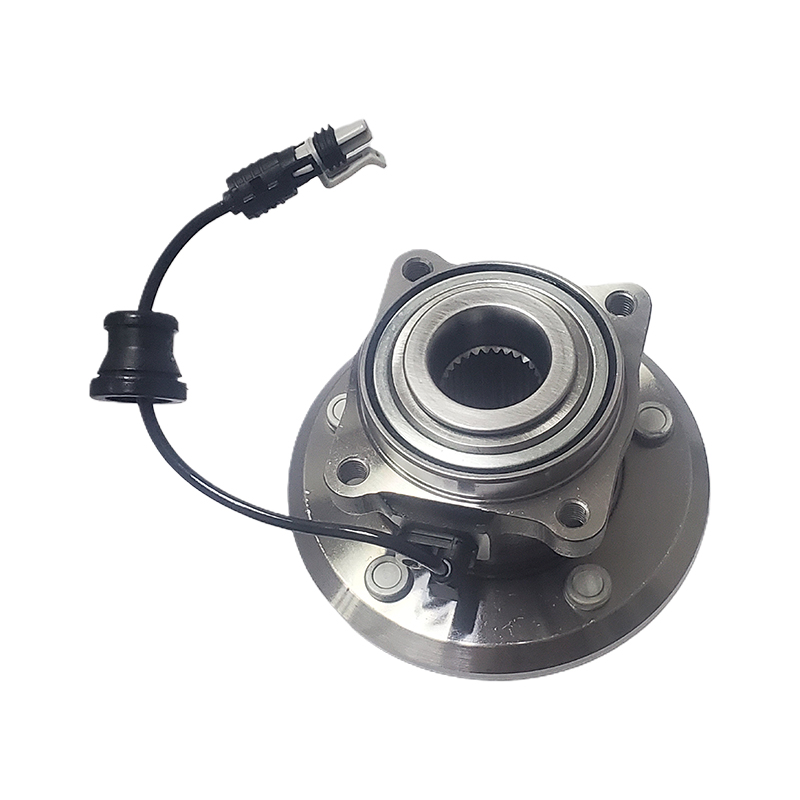
Clutch Release Bearing IEN Europe is a key online source of industry & product news. Find application stories, technical articles, a listing of events & much more!