Dr Jonny Hunter, research & development manager of Fibre Extrusion Technology (FET) discusses how extrusion technology can rise to the challenge of medical grade polymers.
Example of a vertical wet spinning line by FET. Rigid Pvc Extrusion
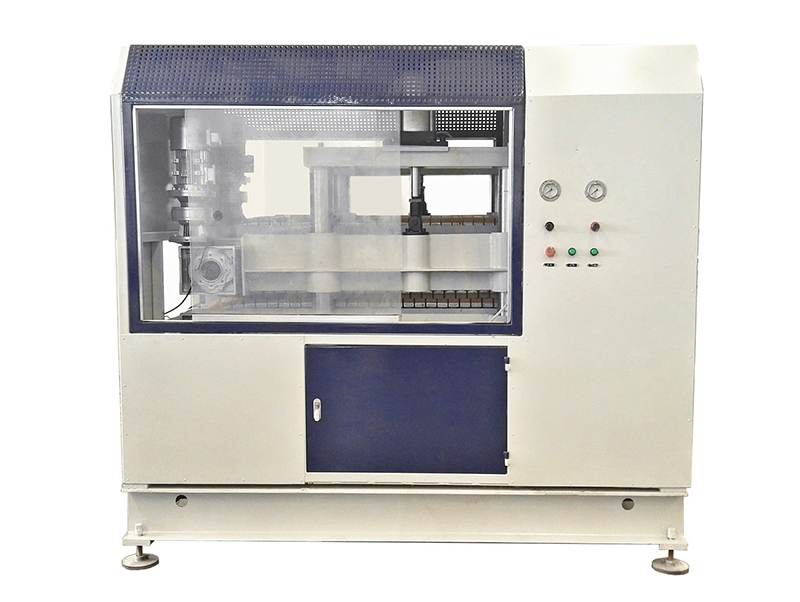
There is a vast array of polymers which are used for medical applications worldwide. FET has processed over 70 different polymer types in multifilament, monofilament and non-woven formats, with many of those being polymers from a sustainable source. This process has involved close collaboration with biomedical research establishments for testing and evaluation.
Modern absorbable sutures are produced, mainly, from synthetic polymers. Most sutures are created as either monofilaments or multifilament yarns which undergo further processing to become sutures.
These are based on a homopolymer or combinations of various block co-polymers. The materials used are PLA - Poly(lactic acid), PGA - Poly(glycolic acid), PCL - Polycaprolactone, P4HB - Poly(4-hydroxybutyrate), PDO - Poly(p-dioxanone) and PTMC - Poly(trimethyl carbonate). These polymers are used due to their high biocompatibility, low toxicity and tuneable absorption rates.
Each building block is subdivided into two types, “hard” and “soft”. Glycolide and lactide blocks are considered “hard” whilst caprolactone, dioxanone and trimethyl carbonate are considered “soft”. The outlier to this trend is P4HB, which does not achieve the same tensile properties as PGA but is far more pliable and flexible than PGA and PLA. It is also capable of stretching up to 10 times its original length before breaking.
A selection of commercial examples of various absorbable sutures.
Regarding extrusion, care must be taken with each of these materials to prevent polymer degradation before/during processing. It is common practice to make sure that the polymer is carefully dried prior to extrusion as these products are very sensitive to degradation via hydrolysis – resulting in significant variation in the intrinsic viscosity (IV) of the polymer, making it unprocessable. Following polymer preparation, FET use a specifically designed combination of extruder and screw to extrude the molten material under an inert atmosphere to achieve the desired product specifications. This really is the key to good quality product.
In addition to this, there is a great deal of know-how on the post-extruder processing of each absorbable suture polymer, which only comes with experience. For example, some of these polymers respond best to a large amount of melt drawing, whilst others achieve the best results through a more step-wise thermal drawing approach. Similarly, when working to produce very fine diameter yarn (10-0 sutures have a diameter of 20 µm) the choice of spin pack, spinneret materials and hole design are cornerstones of any successful production campaign.
FET Monofilament extrusion line used for PDO sutures.
Alongside synthetic polymer-based yarns, there are a number of examples of biopolymers being used as medical products. The market forces surrounding this use of the biopolymers are complex however, one reason for their use is that they are an inherently more sustainable polymer than fossil fuel-based alternatives. For example, P4HB, a recent addition to the absorbable suture market, is produced via bacterial fermentation from renewable sugars rather than chemical synthesised from crude oil – which is the common method for most absorbable suture polymers.
Besides sutures, biopolymers are used in wound dressings, haemostatic agents and in regenerative medicine. The extrusion of these polymers can be challenging as chemical reactions need to take place to produce a fibre rather than a physical, thermal based system. This is where wet-spinning comes into play.
This technology extrudes dissolved solution (dope) through a metering pump into a coagulation bath. In some instances, the dope can become highly viscose and require high torque mixers and vessels capable of reaching high pressure to extrude this material. Historically, this has always been conducted by submersing the spinneret into the solution and conducting the extrusion horizontally.
However, FET have recently developed a vertical spinning system. This line utilises the Venturi effect to allow for better exposure of coagulation media with the dope and easier threading up of the yarn. This is particularly useful when working with more challenging coagulation solutions such as concentrated sulphuric acid or highly basic solutions. FET also supplies Spunbond systems for the scaled development of new nonwoven fabrics based on a wide range of fibres and polymers.
Left: Traditional horizontal wet spinning system. Right: Novel vertical wet spinning system.
Part of Rapid News Group
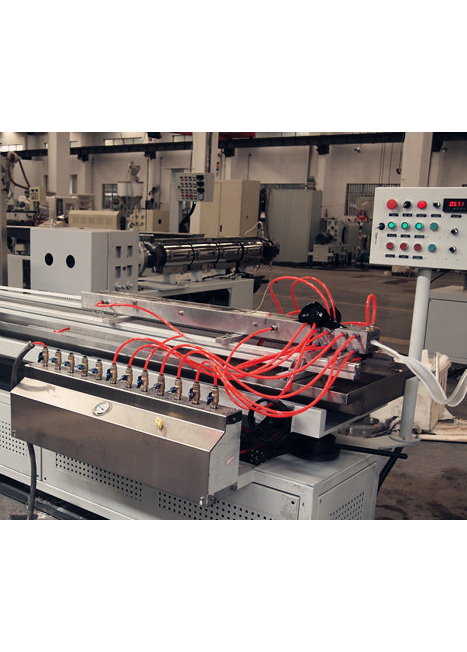
Pvc Pipe Extrusion Plant © Rapid Medtech Communications Ltd. A Rapid News Group Company. All Rights Reserved.