This article is part of the TechXchange: PCB Tools and Technology.
The choice of PCB design is an important factor in determining the mechanical performance of a device. Single-sided and double-sided PCBs currently account for a significant share of the output of boards. This is due to their relatively low cost and fairly high performance levels. PCB Manufacturing
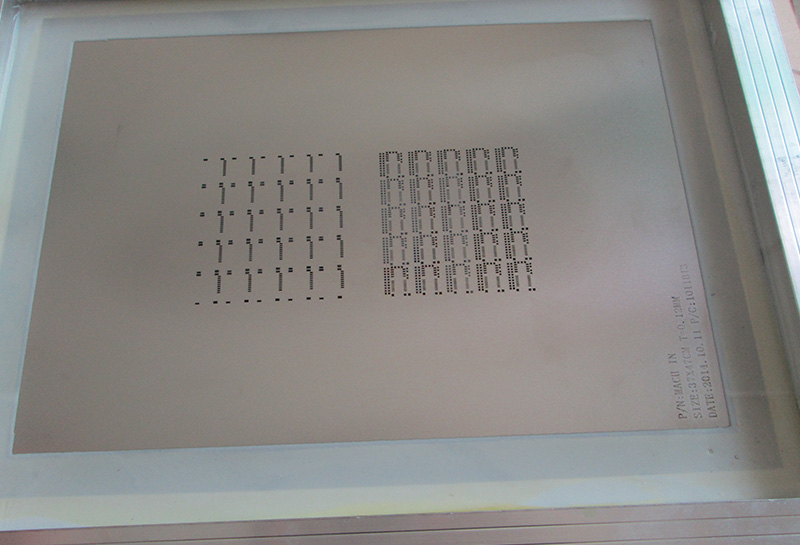
At the same time, high design norms—“conductor/gap”—allow for the use of such boards for the manufacturing of a wide range of modern products. They’re quite suitable for both through-hole mounting and surface mounting.
Flexible substrates used in disk drives and the like are required to withstand bending over 100 million times. Basically, double-sided circuits and multi-layer circuits can’t be repeatedly flexed. If it’s absolutely necessary to bend, it’s necessary to make the bending part a single-sided structure.
It’s said that the layer structure of the bending part of the flexible substrate should be symmetrical with the conductor in the middle. Specifically, a circuit conductor formed from copper foil has an adhesive layer on both sides, a base film, and a coverlay film on the outside. Making the film symmetrical isn't too difficult, but the problem is the adhesive layer of the coverlay.
The adhesive layer is uniform before use, but when laminated on the circuit, it results in poor symmetry. To achieve good symmetry, the conditions for lamination must be considered. In addition, if air bubbles are trapped on the side of the conductor during lamination, those areas will be stressed and thus adversely affect the flex life. Even the smallest air bubbles must be kept out.
The thinner the material, the softer it becomes and the better its flexibility. However, it doesn’t mean that you should make it as thin as possible.
From a practical point of view, it’s said that the best balance is 18 or 12 microns for the copper foil, 12.5 microns for the base film and coverlay film, and 15 to 20 microns for the adhesive layer. However, actual flex life will vary depending on the manufacturer's lamination conditions.
General flexible substrate manufacturers purchase copper-clad laminates and coverlay films from material manufacturers and process them. However, the flex resistance of these copper-clad laminates also varies considerably depending on the manufacturer. In addition, compatibility will differ with coverlay films.
In cases where severe flex resistance is required, it’s also necessary to evaluate the performance of an actual circuit prototype and select a well-balanced combination of materials. Rolled copper foil is said to be better than electrolytic copper foil for the conductor layer, but of late, materials with excellent bending resistance have been put into practical use, so a simple comparison is no longer possible.
Recently, there’s been more cases where copper-clad laminates are forgoing an adhesive layer. Adhesive-free copper-clad laminates are thin because they don’t have an adhesive layer and are generally said to have good bending resistance.
However, a coverlay film material that combines this with a symmetrical layer structure hasn’t been put to practical use. In fact, making the most of the flexibility of adhesive-free copper-clad laminates depends on the performance of each factory.
As mentioned earlier, double-sided circuits should, in principle, avoid repeated flexing. This is because the layer structure isn’t symmetrical with the conductor in the middle. Furthermore, the copper conductor layer, which is plated via hole formation, is hard and brittle.
Even if flexible rolled copper foil is used as the original material when copper is electroplated, it becomes more fragile than electrolytic copper foil. Moreover, there’s a decrease in bending resistance.
Even a double-sided flexible board can be bent to some extent if the conductor circuits on each layer are arranged so that they don’t overlap. The difference in bending resistance depends on the degree of overlap.
It’s most preferable to place the circuit on one layer. If the coverlay film isn’t applied, the symmetry of the layer structure will be enhanced, and it will greatly improve the bending resistance. Even if circuits must be placed on both layers, the circuits should be placed on both sides so that they don’t overlap. If possible, it’s better to provide an appropriate space between the circuits.
Even if double-sided circuits must have bends, certain circuit layouts must be avoided. This involves when one side is a solid pattern, such as a power supply circuit, and the other side is a fine pattern, and the solid pattern is bent inward.
Bending the circuit in such a configuration places a large tensile stress on the microcircuit, and even with a large bending radius, the pattern breaks easily. Good protection of the circuit surface with a coverlay film doesn’t help much, so avoid such circuit layouts at bends.
The stiffness group, the material used, and additional protection against climatic, mechanical, and other influencing factors are determined by following the recommendations of GOST, which are then recorded in the technical requirements of the drawing.
Considerations when choosing the type of printed circuit board:
The base material is selected in accordance with the technical specifications as well as the PCB’s physical, mechanical and electrical parameters. Foiled dielectrics are used in subtractive methods for manufacturing PCBs, and non-foiled dielectrics are employed in additive and semi-additive approaches.
Foil dielectrics used as a PCB base in subtractive methods are composite materials and consist of reinforcing filler, synthetic binder, and copper, aluminum, or resistive foil. The most widely used at present are getinax, fiberglass, polyimide, etc.
Foil getinax consists of compressed layers of electrically insulating paper (reinforcing filler) impregnated with phenolic or epoxyphenol resin as a binder, lined with copper foil on one or both sides (for example, GF record -1 or GF-2 means getinax foil, one-sided or two-sided).
The manufacturing process for manufacturing double-sided boards, as well as single-sided, is part of a more general process for manufacturing multi-layer PCBs. However, many operations aren’t used for the manufacturing of single and double-sided boards. Technologically, they are much easier to manufacture, which favorably affects the production time and price.

Copper Layer Pcb Read more article in the TechXchange: PCB Tools and Technology.