This website uses cookies primarily for visitor analytics. Certain pages will ask you to fill in contact details to receive additional information. On these pages you have the option of having the site log your details for future visits. Indicating you want the site to remember your details will place a cookie on your device. To view our full cookie policy, please click here. You can also view it at any time by going to our Contact Us page.
Traditionally, bus bars are stamped and bent, but stamping cannot always deliver the features required to navigate around the under-bonnet complexity of new-generation EVs. For this reason, bending machines are a far better proposition. “Battery advances and high voltages mean that bus bars are just as at home under the bonnet as they are in a control cabinet backplane,” explains Emma Burgon, Engineering Director at William Hughes. “But automotive applications are not quite as smooth sailing as their significantly less complex industrial peers. As well as electrical insulation, the copper has to be protected from Mother Nature too, which is why the efficacy of the insulation covering is so important.” The development has been driven by the relative ease with which straight copper bar stock can be more easily coated than bar that has already been shaped. But it is possible to over stress the coating and cause stretches and cracks if the material is bent too far or too tightly. For this reason, significant research and development efforts were expended on formulating the capabilities and limits of the materials and the processes. Using bending machines, the minimum bend radius for the high edge is approximately the same as the material’s height, while the minimum radius for the small edge is approximately the same as the material’s thickness. 90° twisting is also possible for confined areas where a bend could be problematic. In all instances, William Hughes can work with customers to help define the material cross section, the bend radii, the curve forms and the geometry possibilities based on the installation space. “As a market leader in springs and wire forms, with many customers in the automotive industry, EV bus bars were a natural evolution of our capabilities,” Burgon explains. “We spotted the market requirement for this a few years back and never being one to shy away from innovation and new markets, we started developing the process and procedures based on the technologies we had in-house. Additional capital assets have since boosted these capabilities, and we are now in a very strong position to serve the needs of the global EV market.” Plug-In Busway
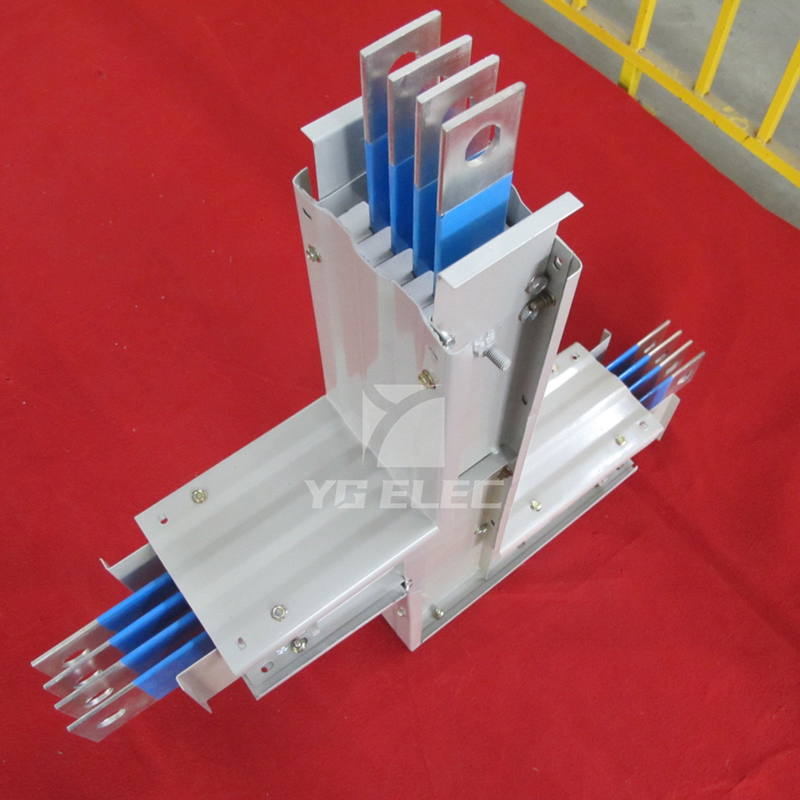

Flame-Resistant Busbar Print this page | E-mail this page